Pilot purgatory is a common problem that organizations face when implementing new technologies such as computer vision in their operations. Manufacturing is no different and in many cases, projects get stuck in the pilot phase for multiple years before dying off due to the high risk of implementation in production.
There are 5 crucial steps that manufacturing organizations should consider when implementing new technology such as computer vision into their production operations to ensure that the technology can scale beyond the pilot phase and into production.
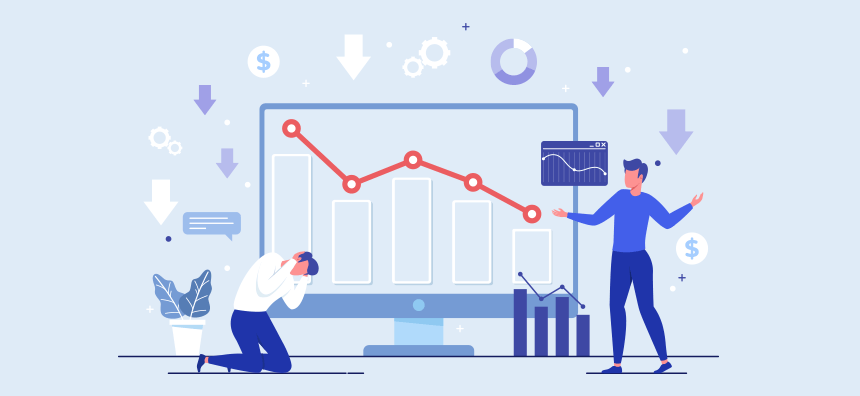